Boost Efficiency: Digital Apprenticeship Tracking & Cloud Tool Management (2025)
A Texas construction crew learned the hard way last year when they lost $500K worth of tools during a storm. Thankfully, their cloud-based tracking recovered 95% of assets within hours. Stories like this explain why 53% of businesses now use cloud systems for equipment management, which is a 7% jump since 2024 1. These platforms aren't just emergency backup plans anymore, but they’re reshaping daily operations. Companies adopting them report 23% less downtime and near-elimination of manual tracking errors 23. Let’s explore how combining digital apprenticeship tracking with cloud tools drives this transformation.
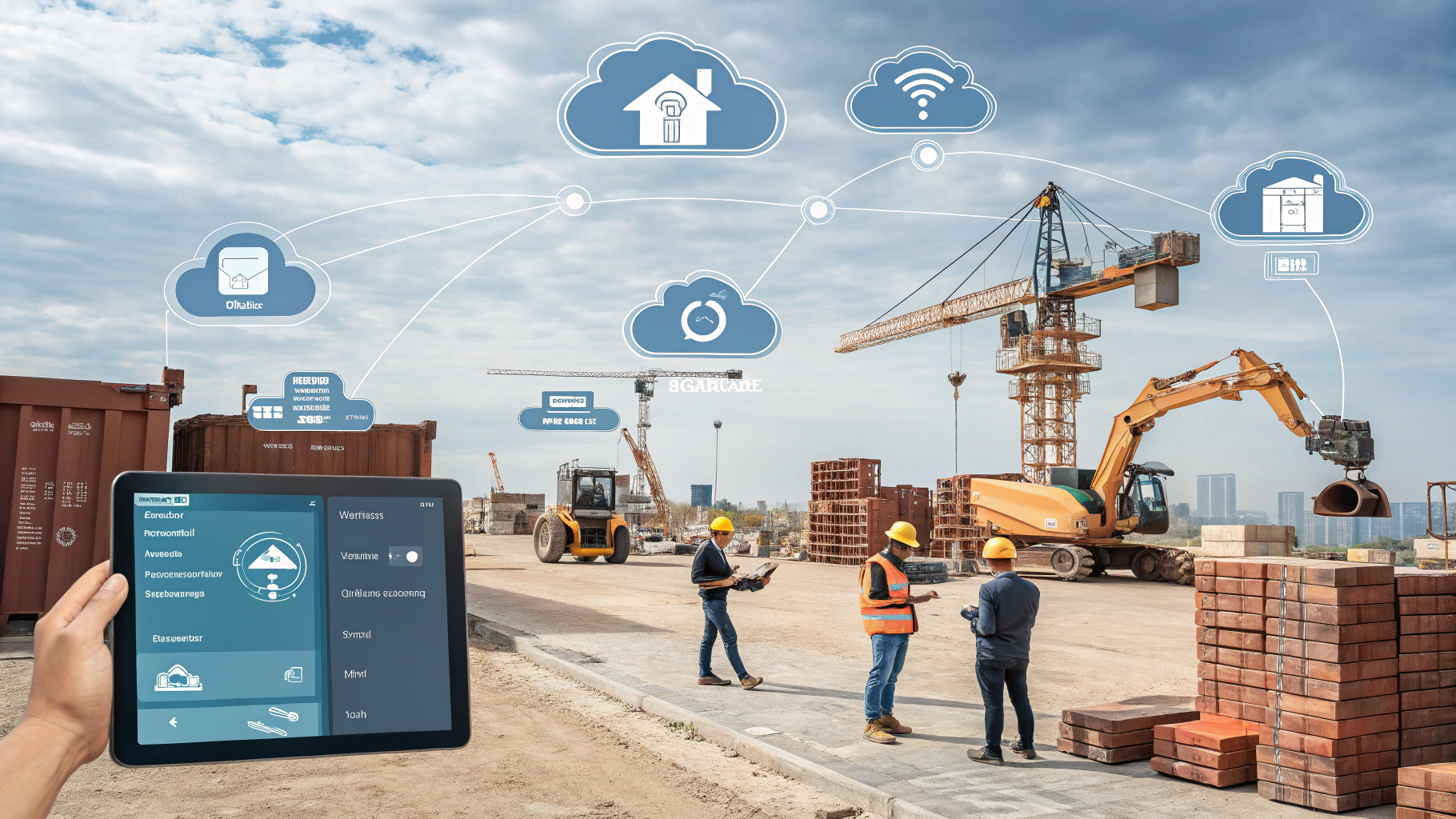
3 Cloud Equipment Tracking Wins for Digital Apprenticeships
Real-Time Visibility Cuts Costs
Cloud systems let teams check inventory levels, maintenance histories, and equipment status from any device. A HVAC technician can confirm part availability mid-repair using a phone, while managers approve orders remotely—no more delays from mismatched spreadsheets 4. For industries like manufacturing, this accessibility slashes equipment delays that once cost $1.5M yearly.
Predictive Upkeep Beats Breakdowns
Gone are the days of waiting for machines to fail. Smart sensors now detect issues like abnormal vibrations or overheating, triggering alerts before disasters strike. One automotive plant avoided $200K in losses by fixing a conveyor belt motor warned by IoT monitors 5.
Grow Without Growing Pains
Small firms once struggled to scale during busy seasons due to server costs. Cloud tools like Oracle’s inventory management now adjust storage automatically. A Midwestern plumbing company expanded to three new states without buying a single server, using real-time updates to track tools across job sites 6.
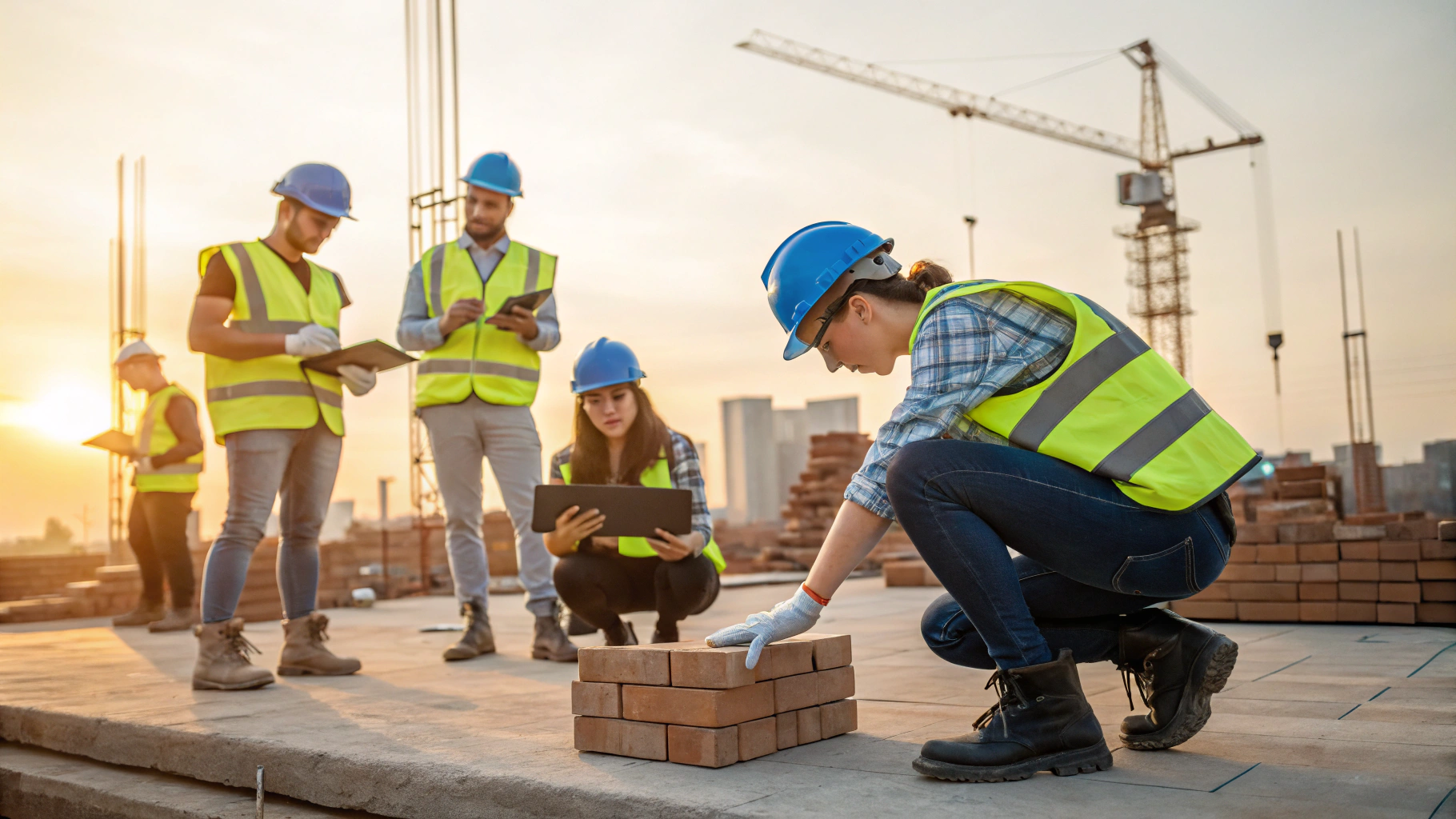
Digital Tool Inventory Strategies Cutting $1.5M Waste
Sync Every Warehouse Instantly
RFID tags and barcodes update stock counts across locations in real time. When a Denver warehouse ran low on industrial drills, the system rerouted supplies from Chicago, saving $18K in expedited shipping fees 4.
Smart Reordering Saves Cash
Machine learning predicts demand spikes using weather data and past sales. After a heatwave prediction, an HVAC supplier stocked 30% more units in Texas, preventing $47K in lost sales 8.
Automate the Grunt Work
Low-stock alerts, auto-generated invoices, and instant reports save 15+ weekly hours. “We reinvest that time coaching apprentices,” says a construction fleet manager who cut paperwork by 60% 6.
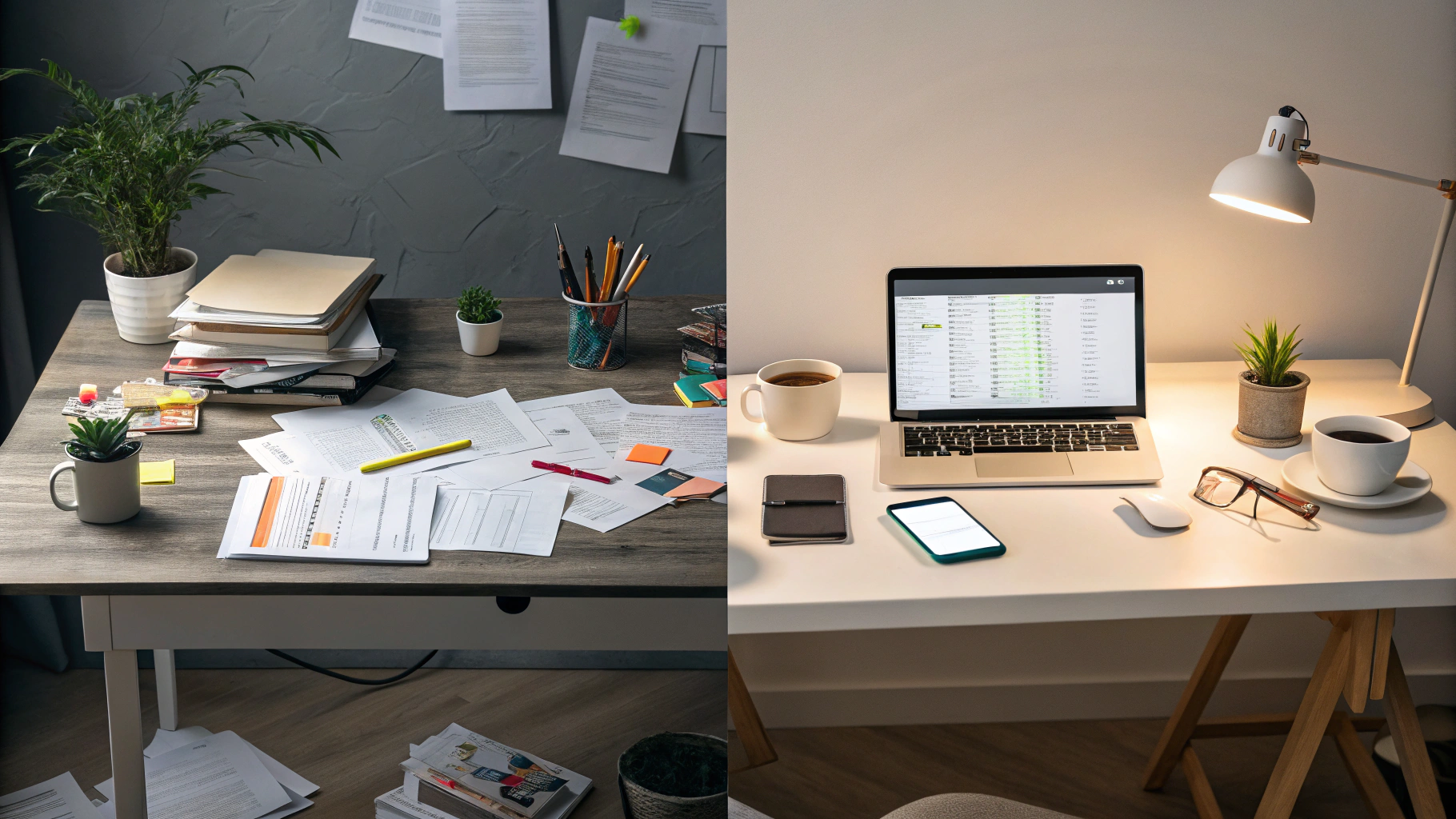
Bridging Skills Gaps Through Apprenticeship Tech
Track Progress, Not Paperwork
Platforms like Apprentice.io link training modules to actual tool usage. When welders in training skipped safety steps, supervisors received instant flags, reducing workshop accidents by 33% 10.
Fix Weak Spots Faster
Analytics revealed electrician apprentices struggled with diagnostic tools. Revised training focusing on common errors cut certification time by 3 weeks, saving $18K per trainee 11.
Beating the “Lost Tool” Tax
GPS Tags Save Millions
After a pharma lab lost 42% of microscopes yearly, GPS trackers pinned each to specific storage rooms. Losses dropped to 6% in three months 12.
Smart Maintenance Schedules
A delivery fleet used cloud data to optimize brake inspections. Fewer breakdowns and better routes saved $1.2M annually 13.
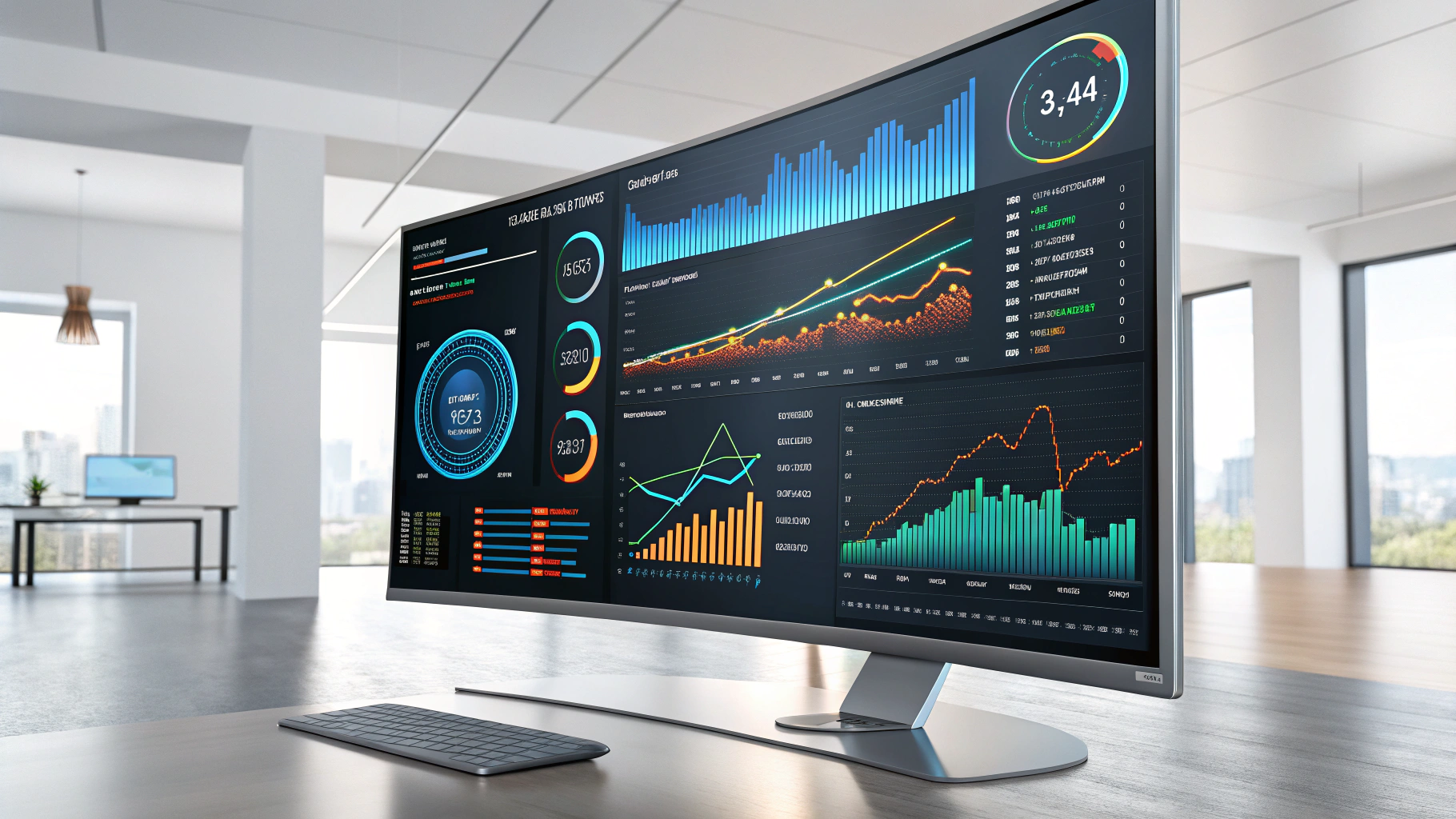
Small Businesses Punching Above Their Weight
From Chaos to Control
A 10-employee plumbing company ditched spreadsheets for Sortly’s tracking system. Real-time updates helped them bid on larger projects, doubling revenue in 2024 6.
Affordable Tech = Fair Fights
With tools like Wasp Barcode ($49/month), startups compete on speed. One garage cut customer wait times by 70% using live parts tracking 15.
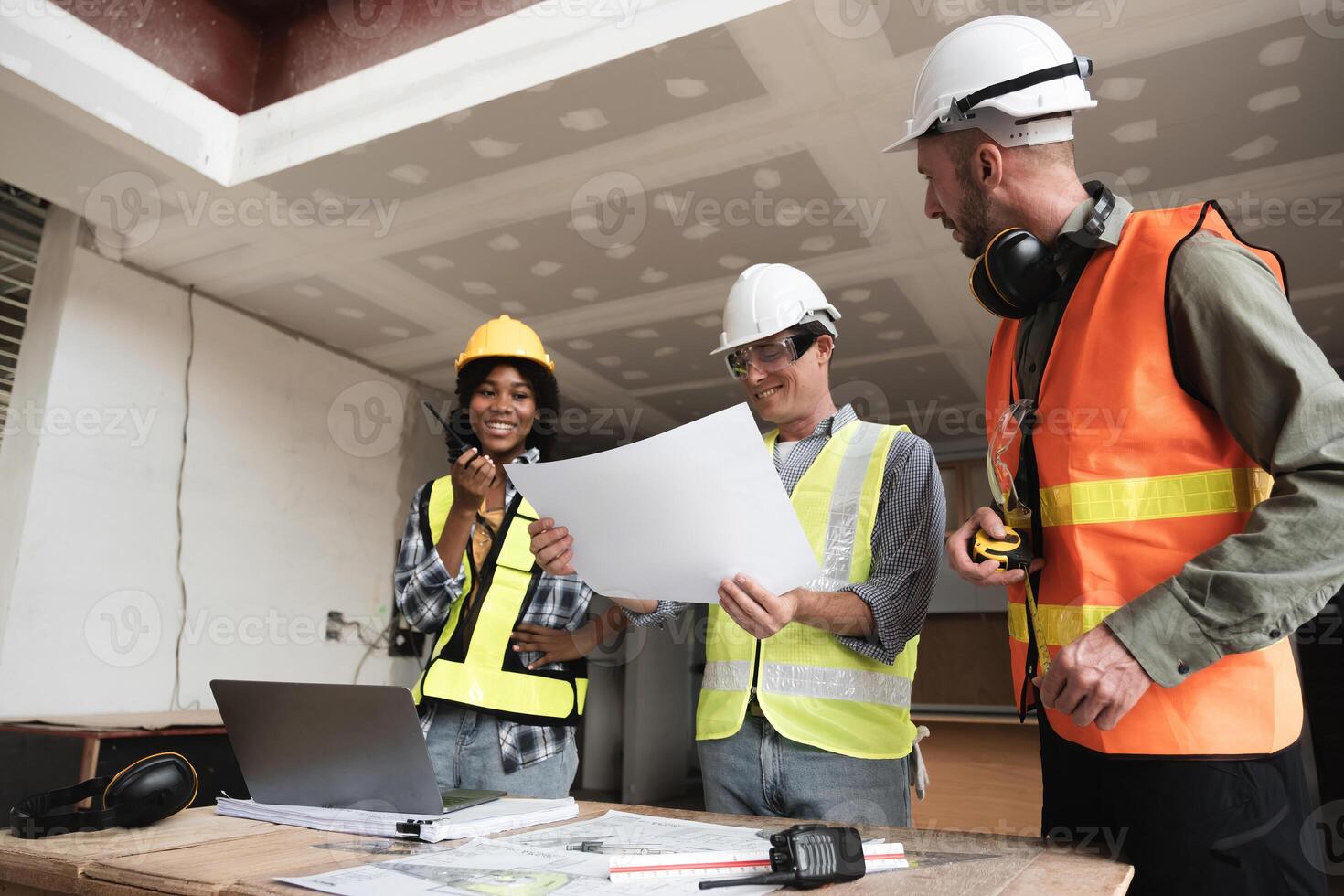
Solving Cloud Migration Head-On
Lock Down Hybrid Systems
When a retailer’s ex-contractor caused a 2024 breach, tightened access controls stopped repeat attacks. Role-based logins now restrict sensitive data to certified staff 16.
Step-by-Step Success
Migrate in phases: tools first, compliance workflows later. Firms with clear plans see 46% higher success rates.
The Future Is Automated
Blockchain Ends Counterfeit Chaos
Aerospace suppliers now log every drill bit’s history on tamper-proof ledgers. Warranty disputes dropped 80% post-implementation 17.
AI Predicts Tomorrow’s Problems
Early adopters get 14-day warnings on equipment failures. One airline even avoided $2M in delays by pre-replacing a flagged turbine.

Why Wait? The Clock’s Ticking
Cloud-based tool management has become essential for staying competitive. From slashing downtime to nurturing skilled apprentices, these systems turn equipment from liabilities into profit engines. Sure, switching over takes some planning, but when you're looking at 23% better efficiency, happier customers, and fewer headaches, it's worth the effort.
Your competitors are already making this move. The question is: how many setbacks can you handle before you decide to make the leap?